
- #Bipolar Square Wave To Two Level Square Wave Driver Circuit Or
- #Bipolar Square Wave To Two Level Square Wave Generator Circuits Are
Bipolar Square Wave To Two Level Square Wave Generator Circuits Are
Bipolar Transistor Cookbook Part 6. The two most widely used types of transistor waveform generator circuits are the oscillator types that produce sine waves and use transistors as linear amplifying elements, and the multivibrator types that generate square or rectangular waveforms and use transistors as digital switching elements.Any AVR microcontroller based board which follows the standard Arduino schematic and is flashed with the Arduino bootloader can be called an Arduino board. The Arduino is refered to as open source hardware and the Arduino IDE is also open source and anybody can contribute their libraries to the Arduino. All arduino boards should be compatible with the Arduino IDE which can be used to program the Arduino boards. Since the Arduino board can act as a stand-alone system it should have capabilities to take inputs process the input and then generate a corresponding output.
The square wave has a period 2pi, has value +1 from 0 to 2piduty and -1 from 2piduty to 2pi. Duty must be in the interval 0,1.However, the operating conditions such as unipolar or bipolar sine, square and triangle waves have placed new demands on the reliable construction of the insulation of the electronic equipment 3. A microcontroller based system sometimes controls other devices by simply generating pulses of certain frequencies and duty cycle.
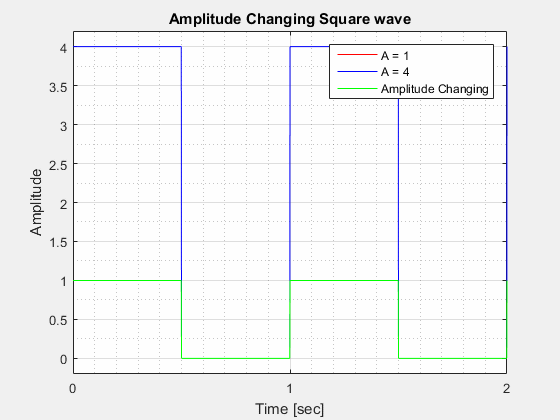
The stepper motor is known for its property of converting a train of input pulses (typically square waves) into a precisely defined increment in the shaft’s rotational position. The motor's position can be commanded to move and hold at one of these steps without any position sensor for feedback (an open-loop controller), as long as the motor is correctly sized to the application in respect to torque and speed.Switched reluctance motors are very large stepping motors with a reduced pole count, and generally are closed-loop commutated.Brushed DC motors rotate continuously when DC voltage is applied to their terminals. When the top electromagnet (1) is again enabled, the rotor will have rotated by one tooth position since there are 25 teeth, it will take 100 steps to make a full rotation in this example.A stepper motor, also known as step motor or stepping motor, is a brushless DC electric motor that divides a full rotation into a number of equal steps.
Bipolar Square Wave To Two Level Square Wave Driver Circuit Or
When the gear's teeth are aligned to the first electromagnet, they are slightly offset from the next electromagnet. To make the motor shaft turn, first, one electromagnet is given power, which magnetically attracts the gear's teeth. The electromagnets are energized by an external driver circuit or a micro controller.
In that way, the motor can be turned by a precise angle.The circular arrangement of electromagnets is divided into groups, each group called a phase, and there is an equal number of electromagnets per group. Each of those rotations is called a "step", with an integer number of steps making a full rotation. From there the process is repeated.
Because of this, stepper motors with more phases typically have more wires (or leads) to control the motor.There are three main types of stepper motors: Permanent magnet motors use a permanent magnet (PM) in the rotor and operate on the attraction or repulsion between the rotor PM and the stator electromagnets.Pulses move the rotor in discrete steps, CW or CCW. For example, if the stepper motor has two groups identified as A or B, and ten electromagnets in total, then the grouping pattern would be ABABABABAB.Electromagnets within the same group are all energized together. The electromagnets of each group are interleaved with the electromagnets of other groups to form a uniform pattern of arrangement.
Whereas hybrid synchronous are a combination of the permanent magnet and variable reluctance types, to maximize power in a small size. Stepping can then be resumed while reliably being synchronized with control electronics.Variable reluctance (VR) motors have a plain iron rotor and operate based on the principle that minimum reluctance occurs with minimum gap, hence the rotor points are attracted toward the stator magnet poles. If current is removed a lesser detent still remains, therefore holding shaft position against spring or other torque influences. This detent has a predictable spring rate and specified torque limit slippage occurs if the limit is exceeded.
Typically, given a phase, the center tap of each winding is made common: giving three leads per phase and six leads for a typical two phase motor. Since in this arrangement a magnetic pole can be reversed without switching the polarity of the common wire, the commutation circuit can be simply a single switching transistor for each half winding. Each section of windings is switched on for each direction of magnetic field.
A quick way to determine if the stepper motor is working is to short circuit every two pairs and try turning the shaft. This is because there is twice the length of coil between the ends and only half from center (common wire) to the end. Resistance between common wire and coil-end wire is always half of the resistance between coil-end wires. One way to distinguish the center tap (common wire) from a coil-end wire is by measuring the resistance. If the terminals of a coil are connected, the shaft becomes harder to turn.
Dithering the stepper signal at a higher frequency than the motor can respond to will reduce this "static friction" effect.A bipolar stepper motor with gear reduction mechanism used in a flatbed scanner.Because windings are better utilized, they are more powerful than a unipolar motor of the same weight. With an H bridge), then remove current from coil A then drive coil B with negative current (again flipping polarity same as coil A) the cycle is complete and begins anew.Static friction effects using an H-bridge have been observed with certain drive topologies. Drive coil A with positive current, then remove current from coil A then drive coil B with positive current, then remove current from coil B then drive coil A with negative current (flipping polarity by switching the wires e.g. There are two leads per phase, none is common.A typical driving pattern for a two coil bipolar stepper motor would be: A+ B+ A− B−. The current in a winding needs to be reversed in order to reverse a magnetic pole, so the driving circuit must be more complicated, typically with an H-bridge arrangement (however there are several off-the-shelf driver chips available to make this a simple affair).
Bipolar with series windings. This kind of motor can be wired in several configurations: Though a bipolar stepper motor is more complicated to drive, the abundance of driver chips means this is much less difficult to achieve.An 8-lead stepper is like a unipolar stepper, but the leads are not joined to common internally to the motor. A unipolar motor has twice the amount of wire in the same space, but only half used at any point in time, hence is 50% efficient (or approximately 70% of the torque output available).
While they are more expensive, they do have a higher power density and with the appropriate drive electronics are often better suited to the application. This method will run the motor on only half the available windings, which will reduce the available low speed torque but require less currentHigher-phase count stepper motors Multi-phase stepper motors with many phases tend to have much lower levels of vibration. Bipolar with a single winding per phase. This requires higher current but can perform better as the winding inductance is reduced. Bipolar with parallel windings.
However, it is winding current, not voltage that applies torque to the stepper motor shaft. This AC voltage is subtracted from the voltage waveform available to induce a change in the current.L/R driver circuits are also referred to as constant voltage drives because a constant positive or negative voltage is applied to each winding to set the step positions. As the motor's rotor turns, a sinusoidal voltage is generated proportional to the speed (step rate). This leads further to the necessity of limiting the current that these high voltages may otherwise induce.An additional limitation, often comparable to the effects of inductance, is the back-EMF of the motor. To overcome the inductance and switch the windings quickly, one must increase the drive voltage. Torque curves may be extended to greater speeds if the stator poles can be reversed more quickly, the limiting factor being a combination of the winding inductance.
